With today’s ongoing competition and global pressures, organizations need to drive innovation and be first to reach the market with new products, ensuring the highest quality at the lowest cost.
Traditional design methods using 2D drawings are mainly central to the product development process and have mainly served as a reference for product definition. Many companies around the globe are increasingly realizing that 2D drawings alone are insufficient and they are prone to design errors and higher manufacturing costs. As a result, companies are looking for new solutions called 3D Master. 3D Master enables the company to find, share, annotate and improve products using the rich format of information - 3D. This approach provides many important benefits, such as the ability to replicate and reuse the product definition for variants, lower cost and improve the quality of the product design and development process and eliminate errors.
Challenges with 2D Drawing
- Difficult to describe a 3D world in a 2D drawing.
- Series of 2D drawings are needed to describe a complex 3D part
- Misunderstandings were common and these often resulted in costly delays and sometimes in the construction of bad parts.
- Many 2D drawings were often required to describe a single 3D part or assembly.
- When design changes were made, a difficult and error-prone process was required which often involved correcting many drawings.
Key benefits of the 3D Master
The latest generation of solid modeling systems makes it possible to insert the dimensions, geometry design and tolerancing, annotations and parts list directly into the solid model, eliminating the need for drawings. Any number of views of the 3D model can be composed, detailed and annotated for specific downstream groups such as manufacturing planning, product services, procurement and marketing/sales. For example, a live 3D model with a prescribed series of annotated and dimensioned views can be provided to a contract manufacturer.
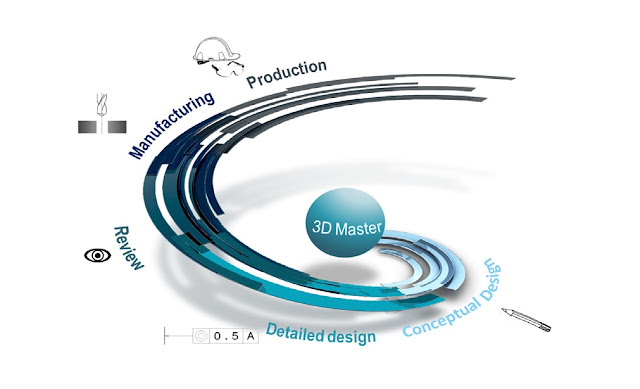
The latest generation of solid modeling software allows easy creation of associative 3D tolerance specifications and annotations. A full set of geometric dimensioning & tolerancing is provided including datum elements and datum targets and text and flag-note annotations to complete the 3D definition. A tolerancing advisor guides the user through the process of putting geometrical tolerances on the part while preventing the creation of an invalid tolerance.
![]() |
3D functional tolerancing & annotations to assist the designer during product definition |
The tolerancing meaning is captured in the dataset to be directly reused by downstream applications such as tolerance analysis, manufacturing or inspection and to check the dimensioning and tolerancing validity throughout the design stage.
The 3D Master can be shared with people across the value chain by providing free or inexpensive lightweight viewing applications. Virtual teams and communities can meet in a real-time environment to search, navigate, chat and collaborate on any aspect of a product-related program. The environment improves decision-making by providing early and direct insight into dimensioning and tolerancing annotations, geometrical elements and features, and the relationships between elements.
- Tolerance and annotations and parts list into a single dataset offer major advantages.
- Confusion over different 2D drawing standards is eliminated because 3D is universal and looks the same to everyone everywhere.
- The 3D Master approach also provides considerable savings in the re-use of product definition information in product families or future versions of the product
- It opens the door to reducing manufacturing costs by opening up unnecessarily tight tolerances.
- The possibility of the geometry, tolerancing and annotations and parts list getting out of sync is nearly eliminated
Conclusion:
Despite the broad adoption of 3D modeling, the 2D drawing remains the primary reference for dimensions, tolerances, and annotations for 90% of manufacturing companies. The central concept of the 3D Master approach is that the 3D product model is the most appropriate vehicle for delivering the detailed product information needed by downstream processes. By converting to the 3D Master method, companies can:
• Define 100% of the product definition using a single 3D dataset.
• Reduce the cost and improve the quality of the product development process.
• Substantially increase the amount of design information that can be re-used in future variants.
• Reduce manufacturing costs by optimizing manufacturing tolerances.
Comments
Post a Comment